金属3Dプリンターによる金型製作の可能性と未来
近年、金属3Dプリンターの技術革新により、製造業におけるプロセスが劇的に変化しています。その中でも特に注目されているのが、金型製作における金属3Dプリンターの活用です。従来の製造方法と比較して、コスト削減、短納期化、設計自由度の向上など、多くのメリットが期待されています。本コラムでは、金属3Dプリンターを使用した金型製作の現状と、その可能性について詳しく解説します。
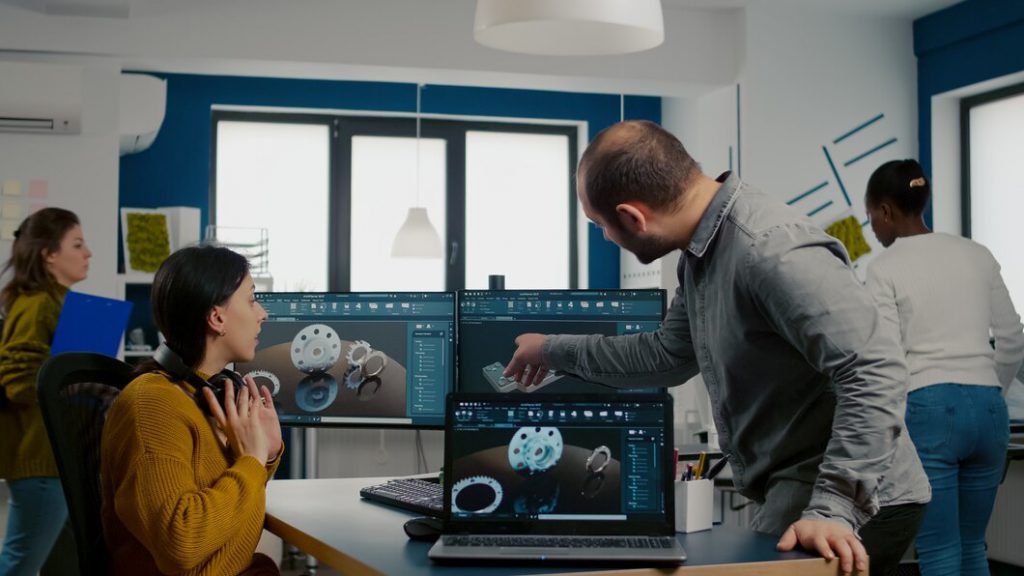
金属3Dプリンターの基礎知識
金属3Dプリンターは、レーザーや電子ビームを使用して金属粉末を溶融し、層ごとに積層していく技術です。このプロセスにより、複雑な形状の部品や構造物を一体で製造することが可能となります。特に、金型製作においては、冷却水路や特殊な形状のキャビティを一体成形することで、効率や品質が向上します。
従来の金型製作との違い
従来の金型製作では、切削加工や放電加工などの工程を経て金型を製作しますが、このプロセスは多大な時間とコストを要します。一方、金属3Dプリンターを使用することで、以下のような利点が得られます。
・短納期化:複雑な加工が不要なため、設計から製造までの期間が大幅に短縮されます。
・コスト削減:材料の利用効率が高く、削り出しによる無駄が減少します。
・設計自由度の向上:従来の加工技術では不可能だった複雑な内部構造(例:コンフォーマル冷却水路)を実現可能です。
3D水管付き金型の利点
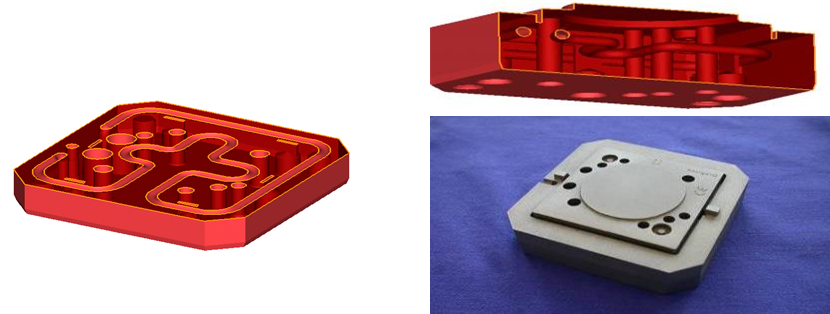
金属3Dプリンターを活用することで、3D水管付きの金型を製作することが可能です。これにより、金型内に効率的な冷却水路を設計することができ、以下のような利点があります。
・成形品の冷却効率が向上し、生産サイクルタイムが短縮される。
・均一な温度分布を実現し、成形品の品質向上に寄与する。
・金型の寿命を延ばすことが可能。
使用可能な材質
金属3Dプリンターで造形可能な材質には、以下のようなものがあります。
・ステンレス鋼
・工具鋼
・アルミニウム合金
・チタン合金
・ニッケル基合金
これらの材質は、それぞれの特性に応じて用途が異なり、金型の性能や耐久性を向上させる選択肢を提供します。
活用が進んでいる業界や分野
金属3Dプリンターは、多様な業界で活用が進んでいます。具体的な活用例を以下に挙げます。
・自動車産業:エンジン部品や軽量化が求められる構造物の製造。特に、冷却性能を高める特殊な形状の金型製作が進んでいます。
・航空宇宙産業:高温に耐える耐熱合金を用いたタービン部品や、軽量かつ高強度な構造部品の製造。
・医療分野:患者ごとにカスタムメイドされたインプラントや手術器具の製造。生体適合性を持つチタン合金が多用されています。
・家電分野:小型で複雑な形状の部品の試作や少量生産に活用され、短納期かつ高精度な製品開発を実現しています。
・電子機器分野:放熱性を高める金型や精密な電子部品の試作に使用されています。
課題と今後の展望
金属3Dプリンターの導入には、いくつかの課題もあります。高価な設備投資が必要であること、製造後の仕上げ加工や品質管理が必要なことなどが挙げられます。しかし、これらの課題は技術の進歩とともに克服されつつあります。
今後、金属3Dプリンターの性能向上やコスト低下が進むことで、中小企業でも導入が容易になり、金型製作のスタンダードになる可能性があります。また、AIやシミュレーション技術と組み合わせることで、より最適化された金型設計が可能となり、さらなる生産性向上が期待されます。
結論
金属3Dプリンターは、金型製作の新たな可能性を切り拓いています。短納期化、コスト削減、設計自由度の向上といった利点は、製造業全体にとって大きなメリットです。これからの技術発展と市場の成熟により、より多くの企業がこの技術を採用し、製造プロセスを革新していくことでしょう。